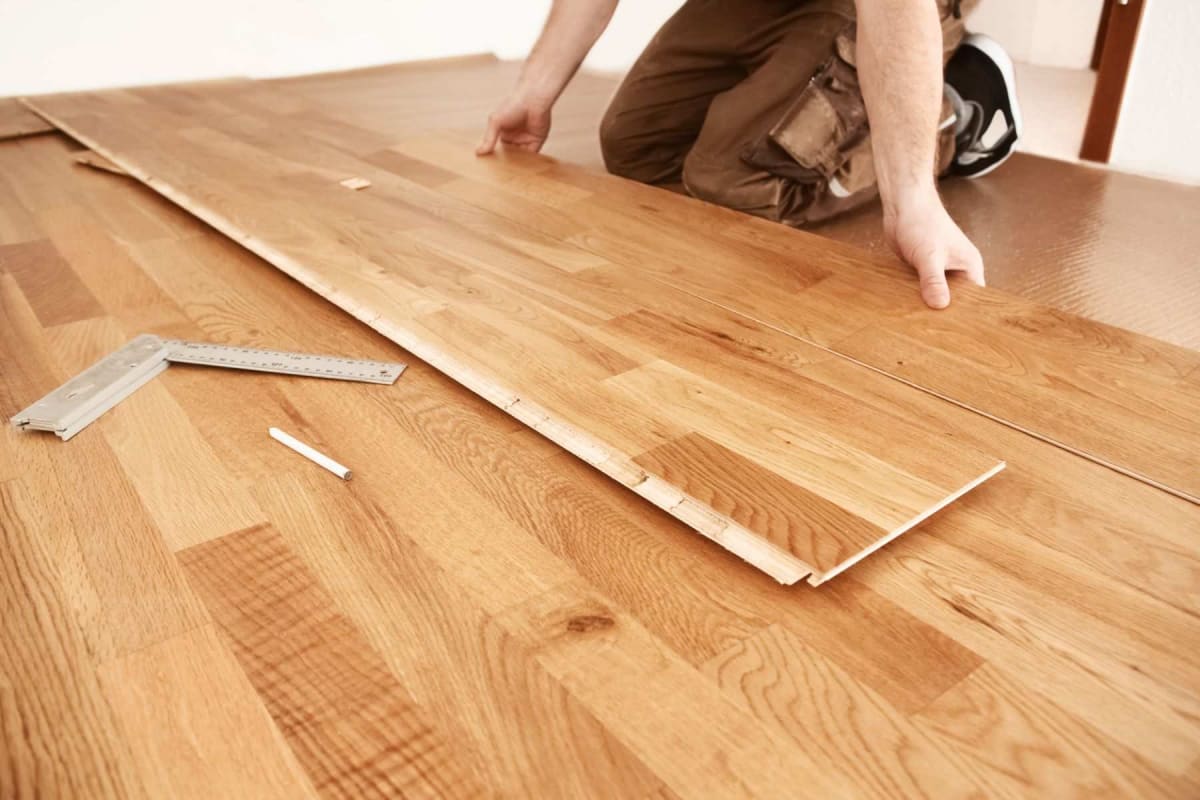
How much does engineered hardwood flooring cost?
How much does engineered hardwood flooring cost?
$9 – $20 average cost per square foot installed
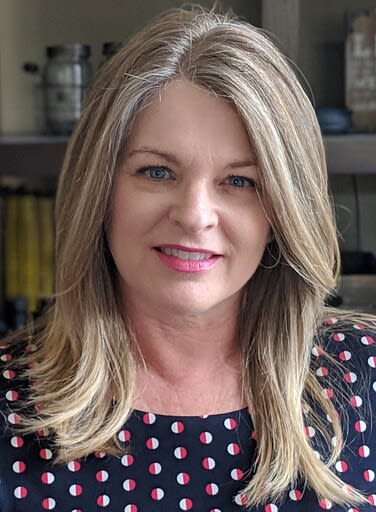
Engineered hardwood flooring cost
Engineered hardwood flooring costs $6 to $12 per square foot for materials alone or $9 to $20 per square foot total to install a mid-range product with 5 core layers. Thinner budget flooring with 3 layers is suitable for low-traffic areas, while high-end materials with 7+ layers offer superior durability and multiple refinishes at a premium price.
Flooring option | Thickness | Material price (per square foot) |
Installed cost (per square foot) |
---|---|---|---|
Budget (3 core layers) | 3/8" | $2 – $9 | $5 – $17 |
Mid-range (5 core layers) | 1/2" | $6 – $12 | $9 – $20 |
High-end (7+ core layers) | 5/8" – 3/4" | $9 – $16+ | $12 – $24+ |
What is engineered hardwood?
Engineered hardwood flooring combines a thin layer of real hardwood with multiple underlying layers of plywood or fiberboard, offering greater stability and moisture resistance than solid hardwood while preserving the natural beauty of wood. The quality and cost of engineered hardwood largely depend on the materials used and how its layers are constructed:
Top wear layer: This is a 2 mm to 6 mm thick veneer of durable hardwood species like oak or walnut. Thicker veneers (4 mm to 6 mm) allow for multiple refinishes and are often coated with tough finishes such as UV-cured aluminum oxide to resist scratches.
Core layers: Several cross-layered plies of plywood or high-density fiberboard (3 or more layers) provide strength, reduce warping, and handle changes in humidity. Generally, the more core layers, the thicker and more expensive the flooring will be.
Backing layer: A moisture-resistant, high-density bottom layer balances the floor and prevents damage by matching the core's expansion and contraction.
Together, these layers create a durable, stable, and attractive flooring option that performs well in a variety of home environments.
Cost of engineered hardwood floors by species
Engineered hardwood typically consists of multiple layers of high-quality plywood topped with a few layers of natural wood. The material cost varies based on the wood type selected. Domestic species like oak or maple provide the best value, while exotics suit luxury spaces where durability and aesthetics justify the premium.
Tree species | Material cost (per square foot) |
Characteristics |
---|---|---|
Bamboo | $2 – $6 | Affordable, termite-resistant, resilient |
Brazilian cherry | $5 – $9 | Exotic reddish tones, high durability |
Brazilian walnut | $5 – $10 | Extremely hard and durable |
Cherry | $4 – $7 | Rich color, ages gracefully |
Cypress | $4 – $6 | Termite-resistant, unique grain patterns |
Heart pine | $2 – $4 | Classic appearance, softer wood |
Hickory | $3 – $7 | Extremely hard, rustic aesthetic |
Mahogany | $6 – $8 | Dark, luxurious finish |
Maple | $3 – $10 | Dense, ideal for high-traffic areas |
Red oak | $2 – $6 | High durability, traditional grain |
Teak | $9 – $13 | Scratch-resistant, naturally water-repellent |
White Ash | $5 – $8 | Light-toned, moderate hardness |
White oak | $4 – $7 | Light color, slightly water-resistant |
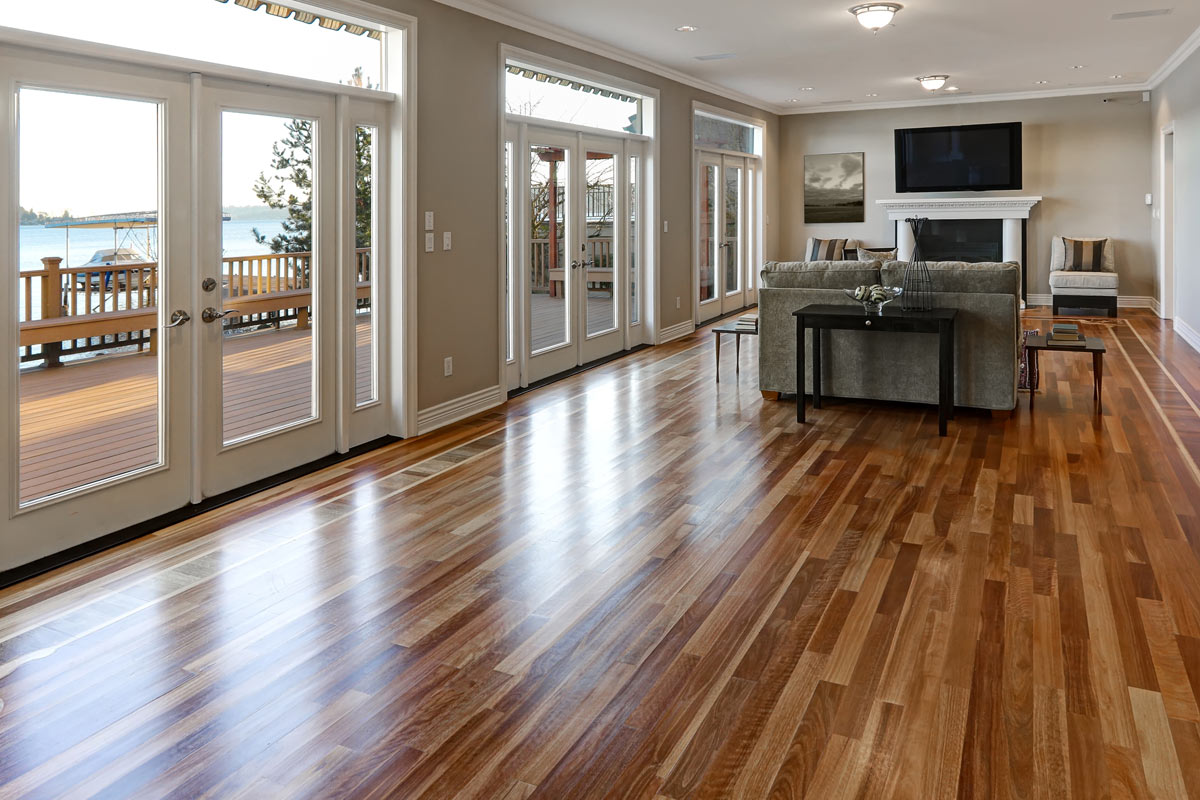
Factors affecting the cost install engineered hardwood floors
Several factors impact the cost to install engineered hardwood floors:
Room size: The size of the room directly impacts the total cost, as larger areas require more materials and labor, increasing the overall price.
Wood species: The type of wood chosen affects material costs, with exotic or harder species generally costing more than common domestic varieties.
Plank thickness & width: Thicker and wider planks typically cost more but may reduce installation time and improve durability.
Installation method: Glue-down, click-lock, or nail-down methods impact labor time and material costs.
Underlayment requirements: Floating installations require underlayment, adding $0.50 to $1.00 per square foot to the material costs for moisture protection and sound dampening. Glue-down/nail-down methods may need specialized moisture barriers or felt underlayment.
Pattern complexity: Complex patterns like herringbone increase labor time and costs compared to simple layouts.
Other factors: Subfloor preparation, waste, and local market demand also affect the final price.
Labor
The Labor cost to install engineered hardwood typically ranges from $3 to $8+ per square foot. The price varies based on the installation method and complexity:
Nail or staple-down installations, common over wooden subfloors, tend to be on the lower end of the labor range. These methods require a plywood subfloor and precise fastening to ensure a secure fit.
Glue-down methods, often required for concrete subfloors or high-traffic areas, usually cost more due to the additional preparation, adhesive application, and moisture-proofing involved.
Click-lock or floating installations are generally the most affordable and popular for DIY projects, as they require less labor and no adhesives. However, floating floors typically need underlayment to provide moisture protection, sound dampening, cushioning, and help smooth out minor subfloor imperfections.
Additional costs
Beyond materials and labor, several extra expenses can affect your overall engineered hardwood flooring project. These additional costs cover preparation, removal, and finishing tasks that are often necessary to ensure a smooth, durable, and attractive floor installation.
Carpet removal costs $0.70 to $1.60 per square foot, or $140 to $320 per room, with glued-down carpet removal being more expensive.
Floor joist repairs range from $500 to over $5,000 depending on the severity of the damage, and they are necessary to prevent structural problems.
Subfloor repairs cost $200 to $1,200 for minor repairs, or up to $6,000 for major repairs.
Engineered hardwood flooring vs. hardwood cost
Solid hardwood costs $11 to $25 per square foot installed. Made from a single piece of wood, it offers long-lasting durability and multiple refinishes but is sensitive to moisture and needs stable environments. Engineered hardwood has a real wood veneer over a layered core, making it more stable, moisture-resistant, and suitable for more areas at a lower price.
Factor | Solid hardwood | Engineered hardwood |
---|---|---|
Average installed cost | $11 – $25 per square foot | $9 – $20 per square foot |
Construction | Made from a single piece of real wood, milled from a tree | Made with a thin layer of real wood glued to several layers of wood products |
Durability | Can be sanded and refinished multiple times, making it last for generations with proper care | The top layer can be sanded and refinished a limited number of times, depending on the thickness. |
Installation | Nailed or stapled to a wood subfloor | Can be nailed, glued down, or floated |
Moisture resistance | Less resistant to moisture – not installed directly over concrete due to moisture issues | More resistant to moisture – can be installed over different subfloors, including concrete |
Stability | More prone to expanding and contracting with humidity | Less prone to expanding and contracting with humidity |
Appearance | More natural appearance | Less natural appearance |
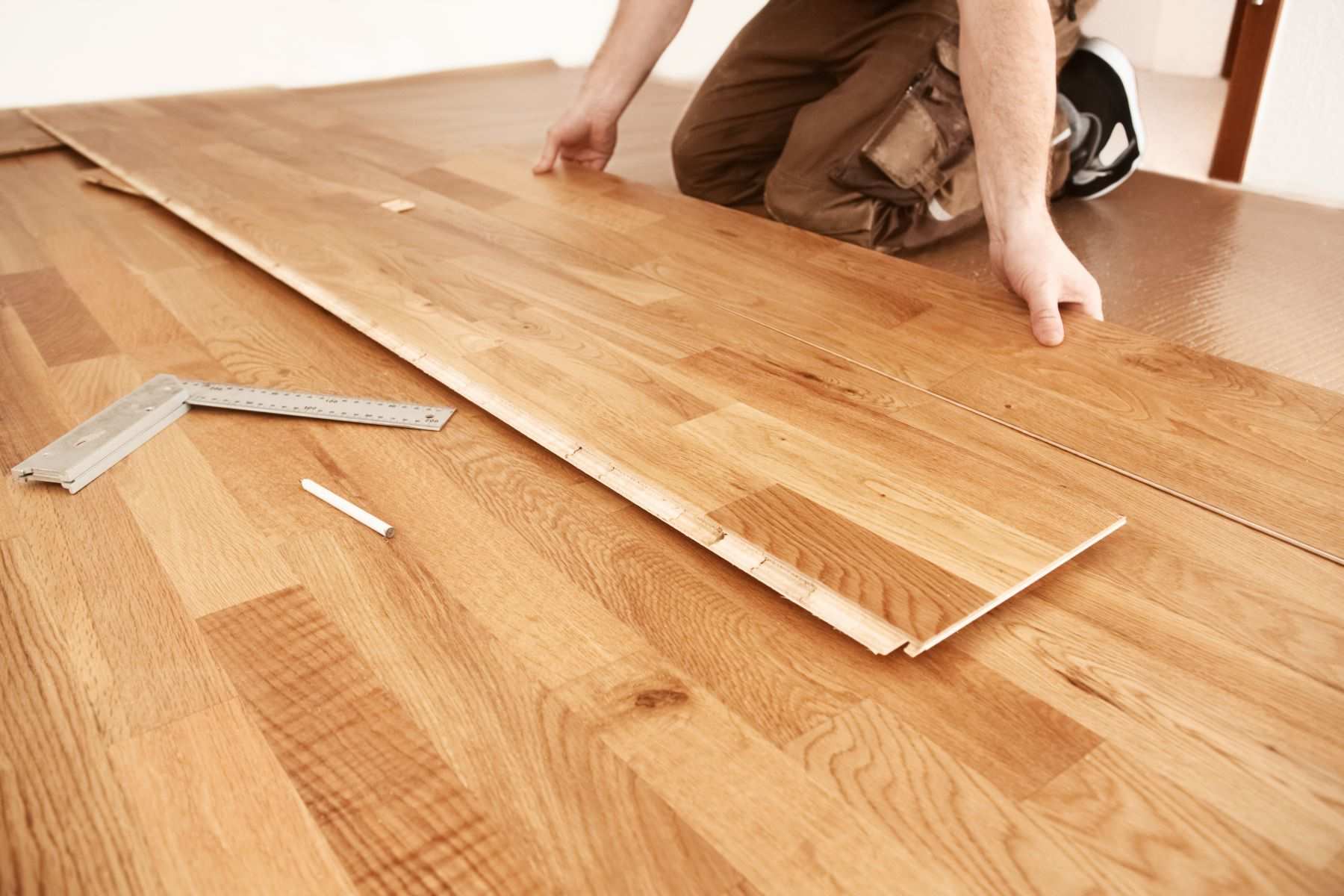
FAQs about engineered hardwood
How do you clean engineered hardwood floors?
To clean engineered hardwood floors, regularly sweep or vacuum with a soft brush attachment to remove dirt and debris. Use a damp microfiber mop—never saturated—and mop along the wood grain, immediately drying any excess moisture to prevent damage.
Can you refinish engineered hardwood?
Yes, engineered hardwood can be refinished, but only a limited number of times depending on the thickness of the top veneer layer. Floors with veneers thinner than 2mm are risky to sand, while thicker veneers allow light sanding to remove scratches and refresh the finish.
Is engineered hardwood waterproof?
Engineered hardwood is not waterproof but is water-resistant to some extent due to its layered construction and protective finishes. It can handle occasional spills if wiped promptly, but prolonged exposure to water can cause warping, swelling, or discoloration.
Is engineered hardwood real wood?
Yes, engineered hardwood isreal wood. It consists of a top layer of genuine hardwood veneer bonded to multiple core layers of plywood or high-density fiberboard, combining the natural beauty of wood with enhanced stability and moisture resistance.
Getting estimates from flooring installers
These tips will help you find a qualified, trustworthy flooring installer and get accurate, comprehensive estimates for your flooring project:
Compare multiple estimates with similar details from different installers.
Verify the installer is licensed, bonded, and insured to protect yourself from liability and ensure professional standards.
Ask for references and photos of past projects to confirm the installer’s experience and quality of work, especially with your specific flooring type.
Request a detailed, written estimate that itemizes all costs including materials, labor, underlayment, subfloor preparation, removal of old flooring, and any extras.
Clarify the installation process and timeline, including who handles furniture moving, cleanup, and who will be your main point of contact.
Discuss the payment schedule up front and avoid paying large sums or cash before work is completed.
Inquire about warranties offered on both the flooring material and installation work.
Be clear about your project timeline and confirm the installer's availability to meet your schedule.
Ask about potential additional costs such as subfloor repairs, moisture barriers, or pattern complexity that may affect the final price.
Questions to ask an engineered hardwood flooring installer
When meeting with installers, ask the right questions to ensure quality work and a smooth project:
Are you licensed, bonded, and insured?
How much experience do you have installing engineered hardwood?
Can you provide references or photos of past projects?
How will you prepare and test the subfloor for moisture?
What type of underlayment do you recommend?
What is included in your installation process and cleanup?
Will you move furniture or appliances?
What warranties do you offer on materials and labor?
Can you provide a detailed written estimate?
What is the expected timeline for the project?
How do you handle expansion gaps and transitions?
Who will be my main point of contact during installation?