
How much does hardwood flooring cost?
How much does hardwood flooring cost?
$11 – $25 cost per square foot installed (solid hardwood)
$9 – $20 cost per square foot installed (engineered hardwood)
$3,500 – $12,500 average total cost for 500 SF
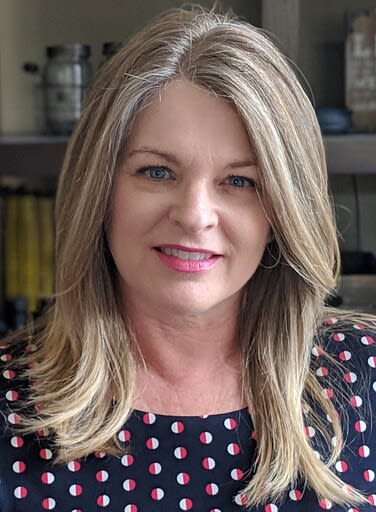
Average cost of hardwood flooring
Hardwood flooring costs $9 to $25 per square foot installed. Hardwood floor prices average $6 to $15 for materials alone, depending on the type and wood species. Wood flooring costs around $1,000 to $6,000 with installation for a single room or $14,000 to $50,000 for a 2,000-square-foot home.
Area size (square feet) | Average cost installed |
---|---|
150 | $1,350 – $3,750 |
250 | $2,250 – $6,250 |
500 | $4,500 – $12,500 |
1,000 | $9,000 – $25,000 |
1,500 | $13,500 – $37,500 |
2,000 | $18,000 – $50,000 |
Hardwood flooring cost factors
The cost of hardwood flooring depends on the type of flooring you install, the size of your space, and the difficulty of the installation. The wood thickness, tree species, wood grade, and plank size also influence the final cost.

Hardwood flooring costs by type
The primary factor that affects the cost of hardwood flooring is whether you install solid or engineered flooring materials. Solid hardwood flooring made from a single piece of wood costs $11 to $25 per square foot installed. Engineered hardwood made of multiple layers costs $9 to $20 per square foot installed.
Factor | Solid hardwood | Engineered hardwood |
---|---|---|
Average installed cost | $11 – $25 per square foot | $9 – $20 per square foot |
Construction | Made from a single piece of real wood, milled from a tree | Made with a thin layer of real wood glued to several layers of wood products |
Durability | Can be sanded and refinished multiple times, making it last for generations with proper care | The top layer can be sanded and refinished a limited number of times, depending on the thickness. |
Installation | Nailed or stapled to a wood subfloor | Can be nailed, glued down, or floated |
Moisture resistance | Less resistant to moisture – not installed directly over concrete due to moisture issues | More resistant to moisture – can be installed over different subfloors, including concrete |
Stability | More prone to expanding and contracting with humidity | Less prone to expanding and contracting with humidity |
Appearance | More natural appearance | Less natural appearance |
In addition to the popular solid and engineered wood, genuine parquet floors and parquet-style tiles are two less common wood flooring options.
True parquet floors use smaller pieces of wood to create a geometric pattern, like herringbone, with the complex installation costing $13 to $40 per square foot.
Prefabricated parquet-style tiles are easier and cheaper to install, with costs ranging from $10 to $16 per square foot installed.

Hardwood flooring prices by thickness
The most common thickness for solid hardwood flooring is ¾" planks, which cost $5 to $15 per square foot for materials alone. This thicker wood is more stable and better withstands wear and tear.
Most engineered hardwoods come in ½" planks, which cost $4 to $12 per square foot for materials alone and are good for medium-traffic areas.
Thickness | Average price per square foot* | Flooring type | Description |
---|---|---|---|
3/4" (19.05 mm) |
$5 – $15 | Solid hardwood |
|
1/2" (12.7 mm) |
$4 – $12 | Solid hardwood or engineered wood |
|
5/8" (15.88 mm) |
$4 – $9 | Engineered wood |
|
3/8" (9.55 mm) |
$3 – $7 | Engineered wood or laminate |
|
1/4" (6.35 mm) |
$2 – $6 | Engineered wood or laminate |
|
*Material price only. Does not include installation.
Hardwood flooring costs by tree species
Different wood species have varying costs based on how they look, how long they last, and how easy they are to find. Woods that are more common and readily available tend to be cheaper, while unique or exotic woods are harder to find and cost more.
Wood species | Average price per square foot* | Description |
---|---|---|
Pine | $3 – $8 | Pine is an affordable softwood that is easy to work with and a good choice for rustic interiors. |
Maple | $4 – $12 | Maple is a hard and dense wood known for its smooth, straight grain and light color. |
Bamboo | $5 – $9 | Bamboo is a grass often used as an alternative to wood since it is durable and resistant to scratches and termites. |
Red oak | $5 – $10 | Red oak is a mid-price wood known for its consistent color and high durability. |
Cherry | $6 – $12 | Cherry is a hardwood with a reddish-brown color best used in low-traffic areas like bedrooms. |
White oak | $6 – $12 | White oak is a domestic hardwood with a light brown color with a straight grain. |
White ash | $6 – $13 | White ash is a hard and strong wood known for its bold, straight grain and light color. |
Hickory | $6 – $14 | Hickory is durable hardwood good for high-traffic areas. |
Brazilian walnut | $8 – $14 | Brazilian walnut (Ipe) is hard and dense with a rich dark brown color and wavy grain. |
Mahogany | $8 – $15 | Mahogany is a mid-priced hardwood with a dark color that ages well. |
Cypress | $8 – $18 | Cypress is a termite and moisture-resistant softwood often used in kitchens and baths. |
Teak | $11 – $20 | Teak is an expensive, hard, dense, and durable wood often used outdoors since it resists moisture and insects. |
*Material price only. Does not include installation.

Hardwood flooring costs by wood grade
Another factor that affects the cost of wood flooring is the wood grade. Wood grade refers to the visual characteristics of the wood, including color variations, knots, mineral streaks, and other natural cosmetic features.
Wood grade | Average cost | |
---|---|---|
Select or clear grade | $$$$ | The highest-quality grade with minimal knots, color variations, and other imperfections |
Natural or No. 1 common grade | $$$ | This grade has a slightly more varied appearance, with some color variations and moderate-sized knots. |
Character or No. 2 common grade | $$ | This grade features a more rustic look with more prominent color variations, knots, streaks, and other natural features. |
Cabin or No. 3 grade | $ | This lowest-quality grade is chosen for a distressed or rustic aesthetic with the most pronounced color variations, larger knots, and other imperfections. |
Hardwood flooring costs by plank size
Finally, the cost of hardwood flooring can also depend on the board length and width, the direction it is cut, and the amount of waste produced.
Wood plank length – The longer the planks, the fewer you will need to cover the same area, saving on material costs. However, longer planks may be more difficult to install, increasing labor time.
Wood plank width – The wider the planks, the more expensive the materials. However, wider planks may save installation time and costs.
Wood milling – The more complex the cut, the more costly the milling. However, the more precise and accurate the milling, the easier the boards will be to install and the better-looking the final installation will be.
Plain-sawn planks are the most common and economical way to cut lumber by making horizontal cuts across the log parallel to its length.
Rift-sawn planks take longer to cut at an angle to the log's growth rings at around 30 to 60 degrees to produce straight grain lines with a more consistent appearance.
Quarter-sawn plants are cut perpendicular to the log's growth rings to produce planks with a straight grain pattern and medullary rays that create a shimmering effect. These boards are worn evenly over time but are most expensive to cut.
Amount of waste – The more milling that is done, the more waste will be produced.

Hardwood floor installation costs
Hardwood flooring materials cost $6 to $15 per square foot. Installation labor adds another $3 to $10 per square foot, depending on the home size and layout, flooring type, installation method, and the installer's experience.
Factor | Average cost per square foot |
---|---|
Materials | $6 – $15 |
Installation labor | $3 – $10 |
Total installed cost | $9 – $25 |
Additional factors that can influence installation costs include:
Home size and layout –Installers often reduce the per-square-foot price when you install a larger amount of flooring. However, they will increase the price when numerous angles and obstacles require precise cutting and fitting.
Installation method – Nail-down floors are the cheapest, while glue-down floors cost more.
Prefinished vs. finished onsite – Traditional hardwood flooring is finished after installation, while a prefinished floor is finished before it is installed. While the upfront costs are higher, there is less mess and lower labor costs with prefinished flooring.
DIY vs. professional – Hiring a professional installer saves time but increases costs. The more experienced the installer, the higher their labor rates but the faster they will work and the better the end result.
Old floor removal – The price to remove old flooring averages $1.50 to $3.50 per square foot, depending on the material. Removing old carpet costs $0.70 to $1.60 per square foot.
Subfloor condition – Depending on the condition, you may need to replace the floor joists costing $350 to $1,000 per joist. Replacing the entire subfloor costs $2.20 to $4.75 per square foot installed.
Finish and coating – When installing hardwood flooring, you need to choose the right finish and coating for the space. The higher-quality the finish, such as UV-cured polyurethane, the more expensive the material costs but the longer the floor will last before refinishing is necessary.
Refinishing and repairs:
Staining hardwood floors costs $0.50 to $2.00 per square foot.
Refinishing hardwood floors costs $2 to $8 per square foot.
Refinishing engineered hardwood floors costs $2 to $6 per square foot, on average.
Hardwood floor polishing costs $40 to $80 for supplies, plus $50 to $80 per hour to hire a local handyman.

Hardwood flooring installation method
There are three common methods for installing hardwood flooring: nail-down, glue-down, and floating. The best installation method for your flooring project depends on the type of wood flooring you're installing, the condition of your subfloor, and your budget.
Method | Average cost | Pros and cons |
---|---|---|
Nail-down | $ |
|
Glue-down | $$ |
|
Floating | $$$ |
|
Pros and cons of hardwood flooring
When deciding on hardwood flooring, you must consider your lifestyle, preferences, and preferred maintenance. Review the pros and cons of hardwood flooring detailed in the following table.
Pros | Cons |
---|---|
|
|

Alternative flooring costs
Hardwood flooring is one of the most long-lasting but costly flooring materials. If your budget doesn't allow for wood flooring, consider one of these other flooring options:
Tile installation costs $10 to $50 per square foot installed.
Laminate flooring costs $4 to $14 per square foot installed.
Vinyl flooring installation costs $2 to $12 per square foot installed.
Luxury vinyl flooring costs $4 to $16 per square foot installed.
Linoleum flooring costs $3 to $11 per square foot installed.
Hardwood flooring FAQs
Do wood floors increase home value?
Yes, wood floors definitely increase the value of a home. In fact, new wood flooring has a return on investment (ROI) of 118% according to the National Association of REALTORS, and hardwood flooring refinishing recovers 147% of the project costs.
How long does hardwood flooring last?
Hardwood flooring can last decades to over a century if it is well-maintained. Solid hardwood can be sanded and refinished to remove surface damage, scratches, and wear. Thicker hardwood can be refinished multiple times, extending its lifespan.
When should I replace my hardwood floors?
Look for these signs your hardwood floors may need replacing:
Floor has already been sanded and refinished multiple times
Deep gouges and scrapes that can't be resolved by refinishing
Visible water damage or structural damage
Warped boards
How do I maintain my hardwood floors?
Clean your hardwood floors regularly with a broom, dry mop, or vacuum. Avoid wet mopping or using liquid cleaners on the floor as this can damage the wood. Consider refinishing wood floors every 7 to 10 years to restore their luster and remove signs of wear and tear.
How do I clean prefinished hardwood floors?
Cleaning prefinished hardwood floors is simple, but using the right cleaning methods and products is important. To properly clean prefinished hardwood, follow these steps:
Sweep or vacuum often to remove dust, dirt, and debris that can scratch the floor's surface.
Spot-clean spills immediately with a dry, clean cloth.
Mop your floors regularly with a mild, non-abrasive floor cleaner and a microfiber mop or cloth.
Avoid excess water, harsh cleaners, steam mops, and abrasive tools.
How do I refinish hardwood floors?
Hardwood floor refinishing requires sanding the surface layer to remove the old finish and buff out any scratches, dings, or discolorations. The contractor can then add a stain to change the wood color if desired. Finally, a clear finish is applied to seal and protect the floor.
Getting estimates from hardwood flooring installers
Installing hardwood flooring is a large investment of your time and finances. Find the right hardwood floor installer near you by following these recommendations:
Compare at least 3 quotes with the same flooring material and installation method.
Pick from licensed contractors with 5+ years of hardwood floor installation experience.
Check out their reviews on HomeGuide and Google.
Avoid selecting the lowest quote that may indicate poor quality materials or workmanship.
Get a written estimate, contract, and warranty before the work begins.
Never pay in full before the project starts. Follow a negotiated payment plan instead.
Questions to ask your hardwood flooring installer
Ask these questions to ensure you find the best installer for your project:
What wood species do you recommend and why?
What installation method do you prefer?
What thickness of wood plank is included in your estimate?
What grade of wood is included in your estimate?
How much do you charge to lay the floor in a herringbone pattern?
What steps will you take to protect the rest of my home during installation?
Does your estimate include removing and disposing of my old flooring?
How much do you charge to move the furniture?
What additional costs can I expect?
Do you offer a warranty policy, and if so, what does it cover?
Is your company licensed, bonded, and insured?
Can you provide a list of references from your past projects?
What financing is available?