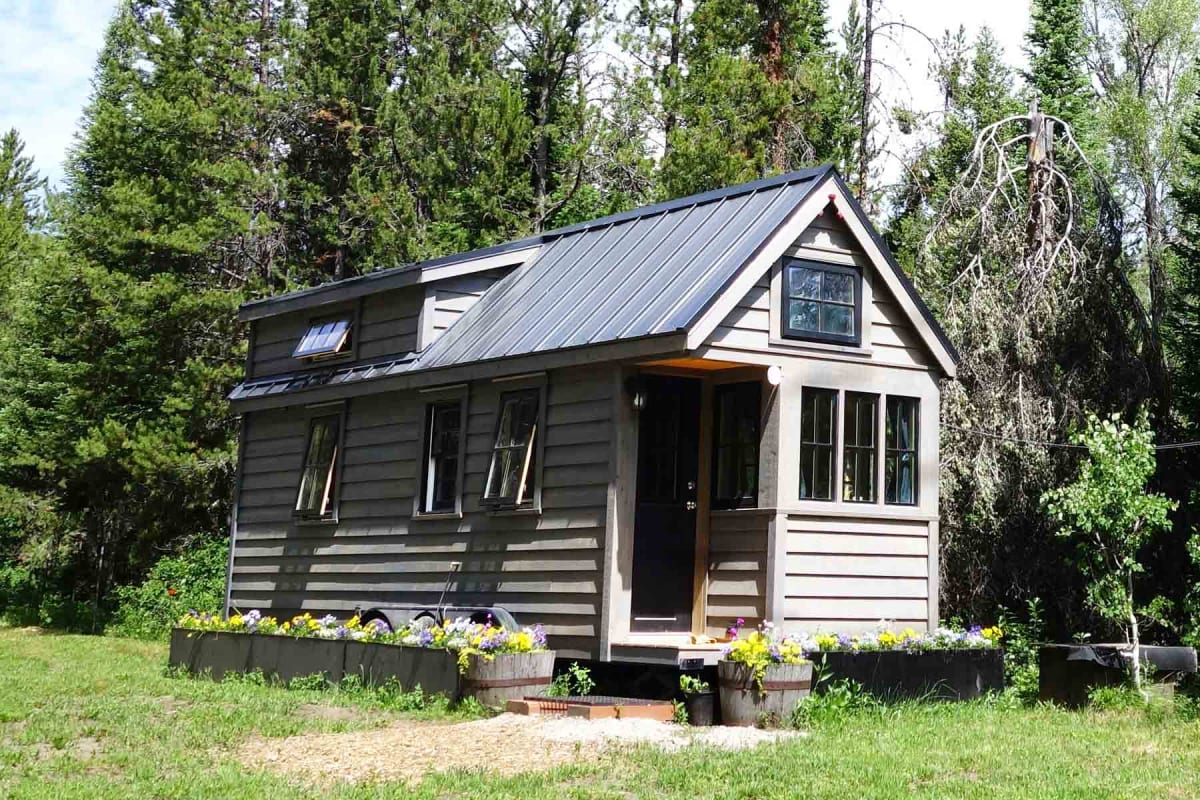
What is the cheapest type of house to build?
What is the cheapest type of house to build?
$75 – $275 average cost per square foot
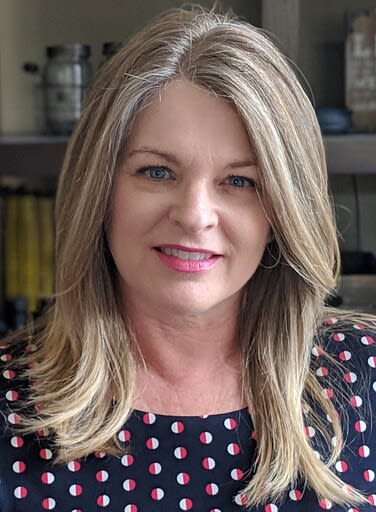
Cheapest type of house to build per square foot
The cheapest homes to build cost $75 to $275 per square foot on average and include barn-style houses, modular homes, shipping container homes, and tiny houses. The cheapest way to build a house is to construct a small home with prefab components, cost-effective materials, and basic finishes.
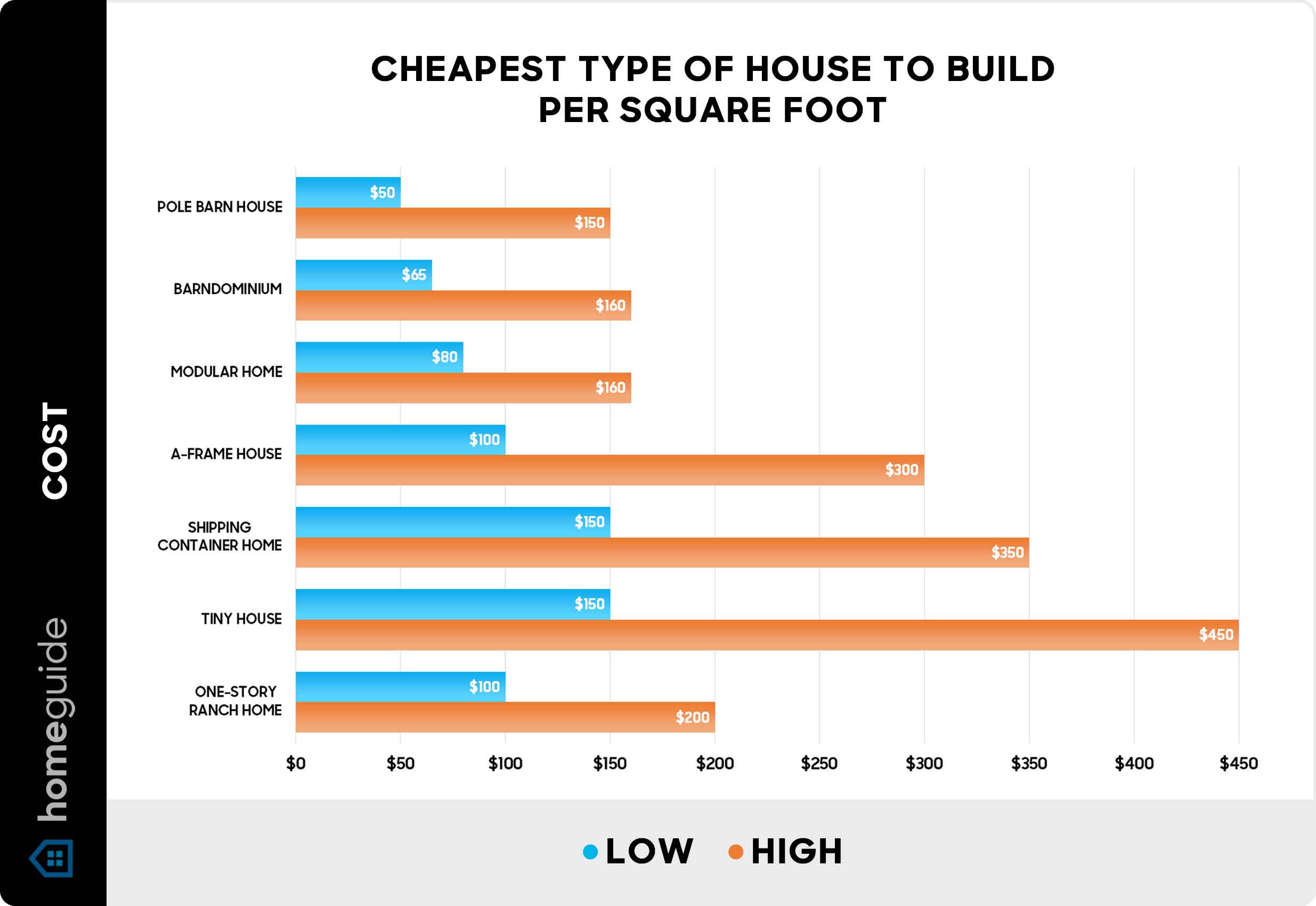
Type of house | Average cost per square foot |
---|---|
Pole barn house | $50 – $150 |
Barndominium | $65 – $160 |
Modular home | $80 – $160 |
A-frame house | $100 – $300 |
Shipping container home | $150 – $350 |
Tiny house | $150 – $450 |
One-story ranch home | $100 – $200 |
As housing prices skyrocket nationwide, many prospective homeowners are seeking affordable ways to build their dream home. Selecting a budget-friendly house style and utilizing cost-effective construction materials and methods can help make owning a new home a reality.
Pole barn house
Building a basic pole barn house costs around $50 to $150 per square foot, depending on the level of finish. Pole barn homes, also known as post-frame homes, are built using poles buried into the ground rather than a concrete foundation. This construction method saves significantly on foundation costs.
Pole barn house kits cost $15 to $40 per square foot for the plans, materials, and labor to assemble the exterior shell structure only. Some companies even offer a complete turnkey package deal that comes complete with interior finishes.
Barndominium
A barndominium costs $65 to $160 per square foot and combines the functionality of an agricultural barn with the livability of a house. Barndominiums take advantage of economical barn construction with simple rooflines, ample windows for daylighting, and a living space that doesn't require load-bearing interior walls.
Barndominium kit prices are $30 to $50 per square foot for the shell and on-site assembly. Site prep, a poured foundation, utilities, and interior finishes make up the remainder of the costs.
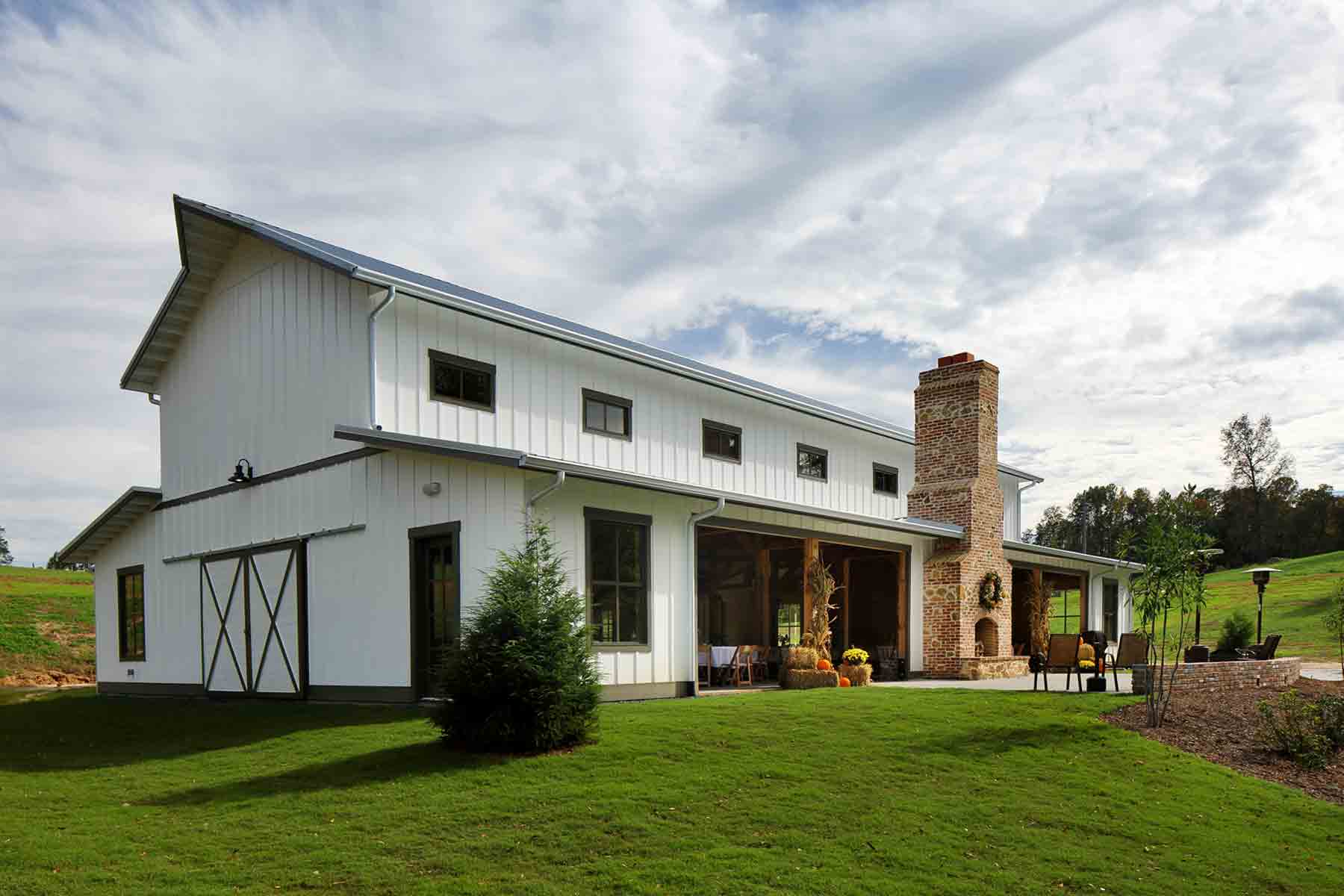
Modular home
Modular home construction costs $80 to $160 per square foot, depending on the floor plan, number of bedrooms, and customizations. The streamlined construction process involves box-shaped sections or "modules" that are built in a factory and transported to your property for assembly, reducing on-site construction costs significantly.
Modular homes offer the choice of pre-designed plans or completely customized homes to meet your desired shape and size. They're built to the same standards as traditional houses with the advantage of less exposure to weather conditions for better quality control and a faster construction timeline.
A-frame house
An A-frame house costs $100 to $300 per square foot to build, depending on whether you purchase a kit or build the house from scratch. A-frames are most popular for cabins, with the steeply sloped triangular rooflines resembling the letter A.
A-frame cabin kits became popular in the 1950s and '60s as a way for families to build an affordable vacation home. The unique shape reduces the home's footprint and materials needed while still providing ample living space across two floors.
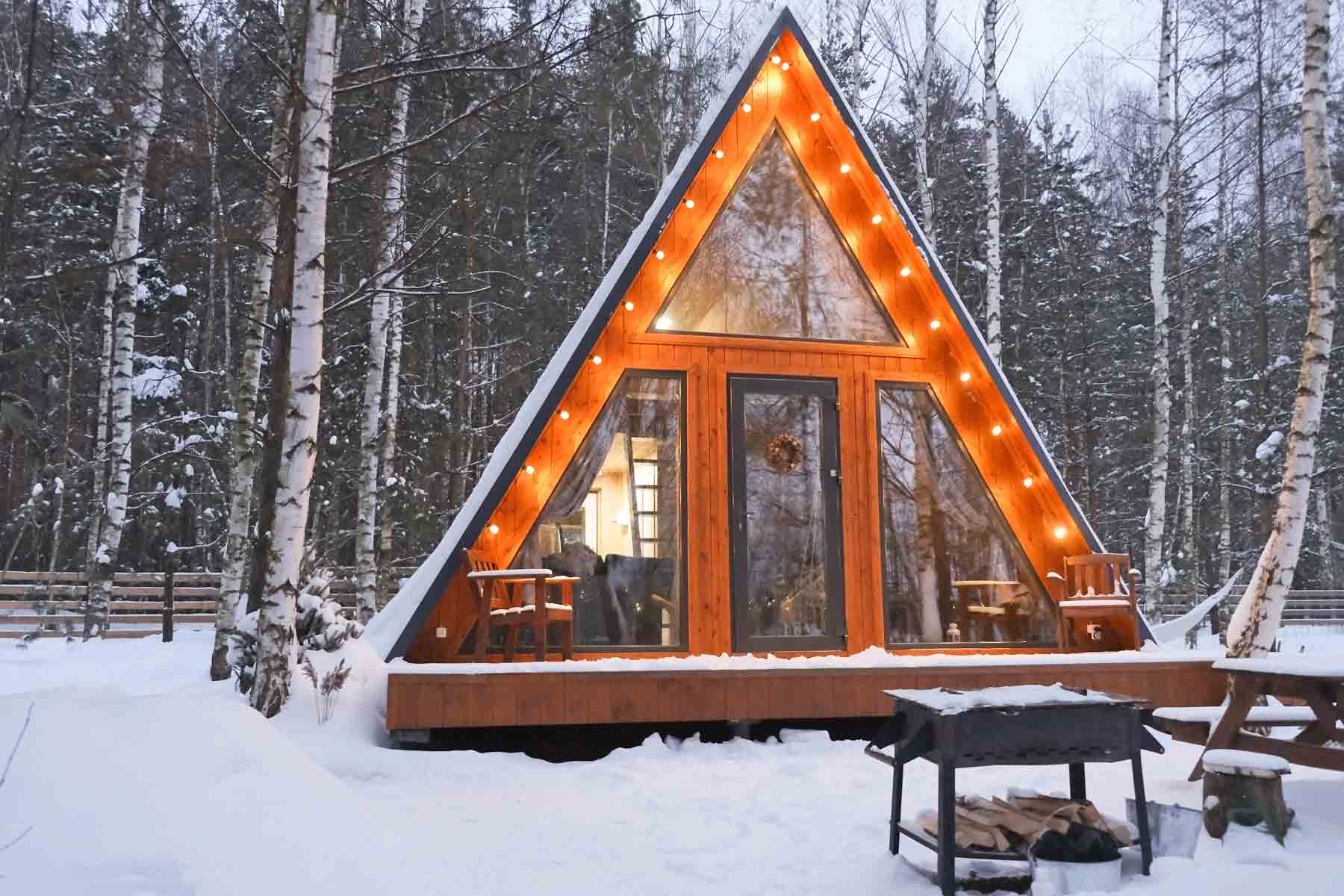
Shipping container home
A shipping container home costs $150 to $350 per square foot for a factory-built prefab container house. Repurposed shipping containers provide an instant structural shell for building a low-cost home. Installing utilities, windows, insulation, and finishes transforms the weatherproof steel box into a livable dwelling.
Shipping containers are typically 8' wide by 8.5' high and come in lengths of 10, 20, or 40 feet. Multiple containers can be combined to increase the living space. Custom container designs by an architect or designer cost $250 to $400 per square foot to build but offer more flexible size, layout, and finishing options.
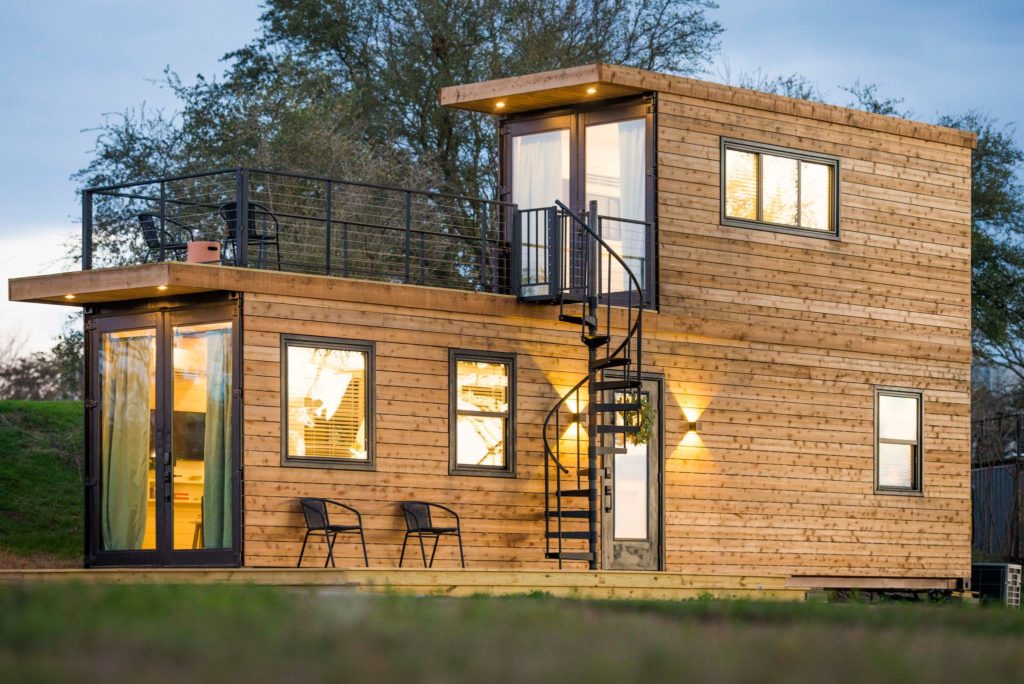
Tiny house
A tiny house is affordable to build, generally because of its compact size of under 400 square feet. The average cost to build a tiny house is $150 to $250 per square foot for a prefab unit or $250 to $450 for a custom-built home.
While tiny houses are extremely affordable, they are not permitted in some areas. Tiny houses built on trailers may bypass zoning rules and high land prices in many areas, but many cities do not allow you to have a tiny home on wheels as a permanent residence.
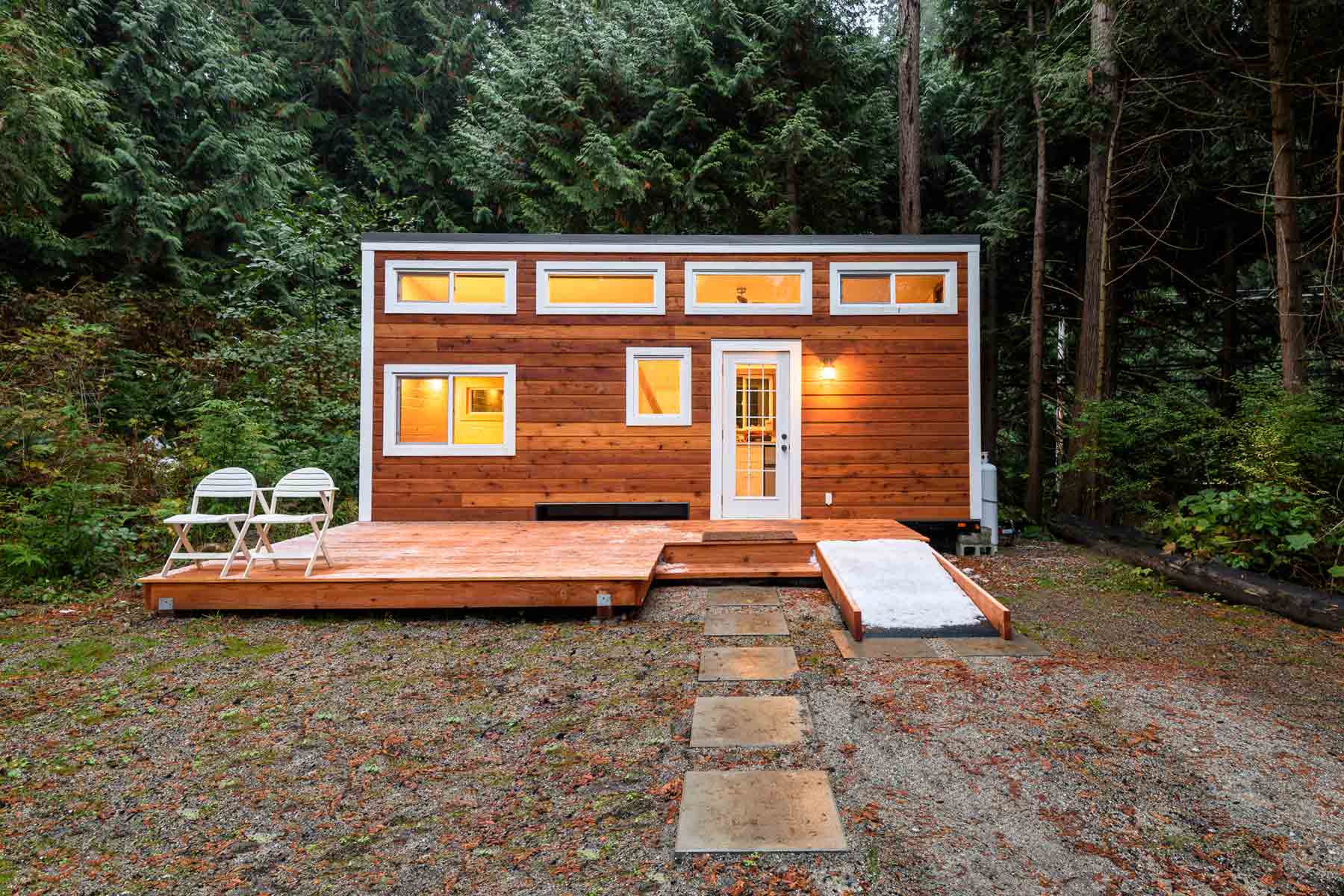
One-story ranch house
Along with those alternative home types, a standard one-story ranch house costs $100 to $200 per square foot to build, making it another cost-effective option. The simple box shape, low-pitched roof, and absence of stairs in a ranch style home keep costs down compared to more elaborate architectural styles.
Ranch houses offer several cost benefits compared to other home styles, including a smaller footprint, simpler and faster construction, and better energy efficiency. Also, the single-story design appeals to a wider range of buyers, increasing the potential pool of buyers and achieving a higher selling price.
How to save money on building a house
The most direct way to reduce your building costs is to keep the home design simple. Complex shapes, bump-outs, dormers, and ornate details all add to material and labor expenses. Instead, opt for a basic rectangular layout and simple roof line to save significantly.
Other cost-saving tips include:
Build smaller – The less square footage you build, the lower your material and labor costs will be.
Purchase prefab components – Companies offering modular kit homes build up to 90% of the house under factory conditions, reducing labor costs and construction delays.
Limit the luxuries – Avoid high-end finishes and the latest smart technologies to trim thousands from your building budget.
Consider alternative building materials – Affordable, eco-conscious materials such as straw bales, cob, or earth bags can reduce your building costs. Recycled and reclaimed materials can also save you money.
DIY when possible – Doing the simplest tasks yourself, such as landscaping, painting, and installing light fixtures and shelves can save you thousands of dollars on labor costs for those services.
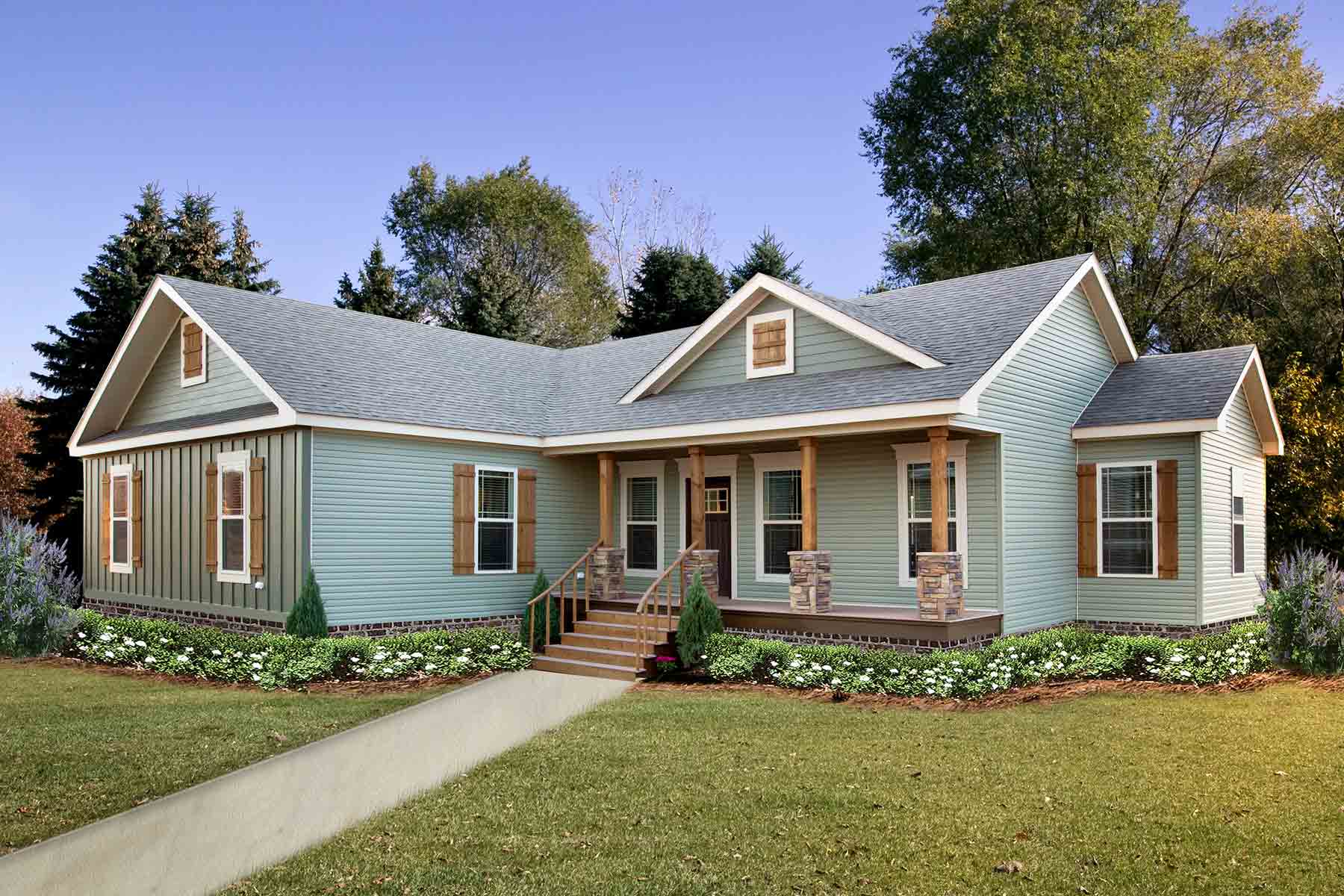
FAQs about the cheapest type of house to build
What is the cheapest type of house to build?
On a per-square-foot basis, pole barn houses and barndominiums are the most affordable at around $50 to $160 per square foot. Other inexpensive home types include modular homes, tiny homes, shipping container homes, and standard one-story ranch homes.
What are the cheapest building materials to use?
The cheapest building materials include plywood, oriented strand board (OSB), and wood framing. Concrete masonry units (CMU blocks) make affordable foundation and walls. Upcycled shipping containers, salvaged lumber, doors, and windows, and basic finishes like vinyl siding and asphalt shingles also provide significant savings.
Is it cheaper to build or buy a house?
Buying an existing house may be cheaper than building a new one because existing homes already have all the infrastructure and finishes in place. Building a new home requires paying for land as well as labor, materials, and construction costs. However, there are situations where building a house might be cheaper:
In areas with low land costs and a surplus of building materials, the cost of building may be lower than buying.
If you have the DIY skills and time to do some work yourself, you can greatly reduce the cost of building a home.
If you have specific needs or preferences that are difficult to find in an existing home, building a custom home could be the more affordable option.
Getting estimates from home builders
To make an informed choice for your home building project, be sure to follow these key steps:
Check reviews from HomeGuide and Google for experienced home builders near you who specialize in the type of home you're interested in:
Ask builders to provide references from past clients you can contact for their perspective on building quality.
Check the builder's credentials, including licensure and insurance in your state.
Have a clear idea of your desired home size, style, and specific features for more accurate estimates.
Don't hesitate to ask about the builder's experience, building process, quality standards, warranties, and payment terms.
Decide on a realistic timeframe and budget before starting home construction.
Questions to ask a home builder
Getting answers to these important questions can help you pick the best home builder for your project:
How long have you been building homes?
Do you have references from past clients?
Are you licensed and insured in my state?
Are there ways to save money by using energy-efficient materials or building practices?
Can you suggest ways to reduce the size or complexity of my home design to save on costs?
What are the financing options you offer, and can you recommend lenders who specialize in affordable housing?
What are the most affordable options for foundations, framing, roofing, and other major components?
Will I save money by using prefabricated components?
Can you suggest ways to simplify the site preparation and landscaping to save money?
Are there ways we can cut costs without compromising quality?